
Alta presión en el cárter.
Una alta presión en el cárter suele ser causada por una excesiva pérdida de presión a través de los aros de pistón, lo que permite que los gases entren en el cárter. Esta condición indica un estado general pobre de la máquina y actúa como una alarma.
👉 Oil Mist Detector – Detector de Niebla en Cárter
El sistema Oil Mist Detector (OMD) o Detector de Niebla en Cárter, es un sistema de protección del motor sumamente importante, es el encargado de protegerlo ante un fallo de temperatura o presión en el cárter por medio de una alarma o en casos de necesidad, un «shutdown» del motor.
El sistema OMD consta de tres partes diferenciadas; el cuerpo, las tuberías que lo comunican con el cárter y los «funnels suction» o embudos de succión localizados en el interior del cárter.
El cuerpo que como se muestra en la foto que adjunto, consta de una escala de leds numerada (0-14) y una serie de leds que indican la opacidad o si se está produciendo algún fallo, más abajo se tratará el funcionamiento del sistema y como leer e interpretar las lecturas de la interfaz del cuerpo.
El cuerpo descansa en un soporte y en sus sujeciones se instalan una serie de «amortiguadores» que absorben las vibraciones transmitidas por el motor cuando este se encuentra en funcionamiento protegiendo así las piezas internas del OMD.
Las tuberías conectan el OMD al cárter, las tuberías salen del cuerpo( una por cada cilindro, si la configuración es en «V» solo se instalan en uno de los lados) las conexiones se introducen en el bloque en la parte alta del cárter.
👉Formación de la Niebla en el Cárter
La formación de niebla en el cárter se puede producir de manera directa; por ejemplo por un fallo en el sistema de refrigeración, o indirecta; por ejemplo daños en partes móviles debido a cambios químicos o físicos en las propiedades del aceite.
➽ Formación Indirecta
Se pueden producir daños causados indirectamente por:
- Desgaste o goteo en partes del cárter, causadas por excesivas horas de operación y falta de mantenimiento. Por ejemplo, unos ejemplos de formación de niebla:
- Desgaste excesivo de los segmentos del pistón por excesiva abrasión como resultado de depósitos de residuos de fuel en las paredes del cilindro que e encuentran a baja temperatura, debido a falta de mantenimiento.
- Los asientos de las válvulas están corroídos por el vanadio contenido en el fuel por emplear un combustible de baja calidad.
Nota: Para saber más sobre los segmentos del pistón: Segmentos del Pistón. Motores
- Daños en partes móviles como se decía al comienzo de este punto debido a cambios en las propiedades físicas o químicas del aceite como resultado de una insuficiente monitorización de la calidad del lubricante. Por ejemplo:
- Daños en rodamientos por cavitación o agua emulsionada en el aceite.
- Daños en las superficies de contacto por corrosión debido a falta de TBN (Total Base Neutral) en el lubricante.
➽ Formación Directa
Se pueden producir daños causados directamente por:
- Condiciones de operación extremas, estas pueden ser internas o externas al motor. Por ejemplo;
- Unas condiciones de operación extrema puede ser el caso de operación del motor con sobrevelocidad, debido a un fallo en el control de la velocidad o a la intervención humana principalmente. Estas condiciones pueden dañar prematuramente el motor y producir rápidamente niebla en el cárter.
- Defectos en el sistema de refrigeración, el resultado se trasmite en las camisas del motor, las cuales denotan un incremento de la temperatura que desencadena una serie de eventos tales como; condensación del fuel y desintegración del lubricante dando lugar a su vez a desgaste y fugas entre los segmentos del pistón con la consecuente pérdida de compresión y entrada de gases de combustión en el cárter, dando lugar a formación de niebla.
- Situaciones de motor en sobrecarga, en caso de sobrecarga del motor, la efectividad de la lubricación se ve mermada dando lugar a más rozamientos y calentamientos de elementos internos dando lugar a la formación de «oil mist»
👉 Condiciones de Operación:
La siguiente fotografía corresponde a la interfaz del cuerpo del Oil Mist Detector y en ella está toda la información que necesitamos, según la configuración de leds que nos encontremos (encendidos, parpadeando o apagados) podemos interpretar que condiciones de operación tenemos:
- Condiciones normales de trabajo
- Condiciones de fallo
- Condiciones de niebla en cárter
___________________________________________________________________________________
NORMAS PARA EL USO Y CONSERVACION DEL MATERIAL DE CASCO, ELECTRICIDAD Y MAQUINAS NAVALES (N O C E M) CAPITULO 22 MOTORES DE COMBUSTION INTERNA
22-129. Posibilidad de explosiones.
a. Si un motor debe pararse por el engrane de un pistón o el calentamiento de un cojinete, no se sacarán las puertas de visita del cárter, ni se pondrá el motor nuevamente en marcha hasta que hayan transcurrido 10 minutos por lo menos y, preferentemente, no antes de que se haya enfriado. La admisión de aire al cárter antes que el motor esté frío, puede causar una explosión.
b. Si ha ocurrido una explosión o ha habido un incendio en el cárter, la concentración de oxígeno dentro del mismo será demasiado pobre para mantener la combustión, pero la fuente de calor puede persistir durante un tiempo y si se saca una puerta del cárter, la entrada de aire fresco podría proveer suficiente oxígeno para producir una segunda explosión o incendio.
ANEXO 22-4
J. EXPLOSIONES EN LOS CARTERS
Son relativamente raras las explosiones en los carters de los motores diesel pero, la gravedad de sus consecuencias, en particular para el personal, obliga a que sean bien conocidas sus causas y en algunos casos, los medios destinados a limitar sus efectos. Por lo general, los daños materiales se limitan a simples roturas de tapas de carter y a posibles incendios en el compartimiento.
La mayoría de las explosiones registradas son debidas a la ignición de una mezcla inflamable, formada dentro del carter, en contacto con una pieza elevada a alta temperatura.
a. Formación de la mezcla inflamable.
En un motor diesel en funcionamiento, la atmósfera de su carter se carga de aceite en suspensión; este aceite puede presentarse bajo dos formas:
1. En pequeñas gotas, debidas a la pulverización como consecuencia del batido del aceite que brota de los cojinetes o que retorna al carter, en especial, por la acción de los aros rasca aceite.
2. Bajo la forma de vapor condensado; el vapor formado por el aceite en las zonas donde éste se encuentra más caliente, se esparce por todo el carter, pero tiende a condensarse en la vecindad de las paredes relativamente más frías.
Estos vapores condensados son los que toman el aspecto de "humo de aceite".
Para formar una mezcla inflamable, el peso de aceite en suspensión en el aire del carter, debe alcanzar un cierto valor mínimo que puede estimarse del orden de los 50 miligramos por litro.
En los carters de los motores en buen estado de conservación y funcionamiento, este límite peligroso, normalmente, no es alcanzado, en razón de que la temperatura de las piezas no es suficientemente elevada como para provocar una importante vaporización del aceite en servicio, porque, además, la tensión máxima de estos vapores es relativamente baja. La situación varía desde el momento en que un cojinete u otra pieza cualquiera se calienta; la vaporización del aceite al hacer contacto con ellas se acelera y hasta puede provocarse volatilización, es decir, en sus cercanías aumenta rápidamente la proporción de vapor de aceite.
b. Inflamación de la mezcla aire-aceite.
Cuando la pieza que se calienta, como ser un cojinete, sobre todo en los motores con bujes de bronce en los pernos del pistón, un eje, una falda de pistón, un buje soporte de una transmisión para accionamiento de una bomba, etc., alcanza una temperatura suficientemente elevada, la violenta inflamación de la mezcla aire-aceite, se manifiesta en forma de explosión.
Esta inflamación, también puede ser provocada por una emisión de chispas al producirse una fuerte engranadura o roce metálico, o por un pasaje de los gases de la combustión dentro del carter, como consecuencia de una rotura o rajadura de un pistón, sobre todo si éstas son de aleación liviana y son fácilmente afectadas por una sobrecarga del correspondiente cilindro, una mala pulverización del combustible el cual actúa de soplete o a una detención de la refrigeración del pistón.
c. Medios para prevenir las explosiones.
Puede parecer deseable impedir que la proporción de la mezcla aire-aceite alcance el límite de inflamabilidad en base a una renovación de la atmósfera del carter por medio de la aspiración de una bomba o de un ventilador. Este procedimiento, debe ser totalmente descartado en razón de que la ventilación que puede realizarse nunca es perfecta y no impide la formación de una especie de nube explosiva en las cercanías de una pieza demasiado caliente que acelera, violentamente, la vaporización o la volatilización del aceite. En caso de inflamación, el calor generado por la combustión de dicha nube hace aún más intensa la vaporización y los nuevos vapores que se forman siguen generándose o inician su combustión mientras quede aire disponible.
Resulta en consecuencia más apropiado y lógico evitar toda ventilación para limitar el peso de aire presente en el carter y reducir la gravedad de las eventuales explosiones. En ciertos casos, la proporción de aceite en la atmósfera del carter puede hacerse superior al límite por encima del cual la mezcla no es más inflamable porque es demasiado rica.
d. Válvulas de seguridad contra explosiones de carter en motores diesel. Ver Fig. 22-5 al final.
Precisamente basados en lo expresado en c., es decir, evitar toda ventilación para reducir la gravedad de las eventuales explosiones, existen actualmente válvulas especiales de seguridad que han sido adoptadas por varios fabricantes de motores diesel. Estas válvulas, dan protección al personal y equipos en caso de producirse una explosión de carter. El resorte liviano y sensible que actúa en esas válvulas, es inmediatamente comprimido y posibilita así que la válvula, al permitir el pasaje del aire-aceite proveniente del carter, reduzca la presión en el mismo. La válvula, al reducir esta presión, se cierra rápidamente para prevenir la entrada de aire al carter.
La posibilidad de una segunda explosión, es así grandemente reducida.
La cubierta de la válvula está diseñada en forma tal que obliga a los gases explosivos a dirigirse al cuerpo del motor para prevenir así su expansión horizontal y proteger al personal. Un drenaje de aceite, vuelve este último, al carter por un sistema de sifón.
El motor lleva una válvula por cada cilindro.
En la figura se ve, en la mitad izquierda, la válvula cerrada, con su disco ondulado asentando en el aro empaquetadura y el resorte expandido.
La parte derecha muestra la válvula totalmente abierta. La gran área libre de pasaje de esa válvula, deja escapar el gas a la atmósfera sin restricciones. Asimismo, la parte izquierda de la figura muestra la válvula sin el aro de fijación del conjunto, el que puede ser montado sobre la parte externa de la las tapas del carter por medio de bulones.
En la figura del lado derecho, también se ve 1a válvula abierta y el aro de fijación de conjunto.
Estas válvulas deben ser inspeccionadas y verificadas antes de poner en marcha el motor, asegurándose de que pueden funcionar sin dificultad, es decir que el resorte acciona bien y que la válvula está libre y asienta correctamente sobre la empaquetadura asiento.
e. Vigilancia de los carters.
Por lo general, los carters tienen conductos de desahogo de los vapores del aceite que evitan la acumulación de presión proveniente de los gases "soplados" a lo largo de los pistones, en particular cuando no disponen de las válvulas de seguridad descriptas en el punto d.
Estos conductos, como las válvulas de seguridad mencionadas, constituyen excelentes testigos cuando hay variaciones importantes por sus descargas.
Normalmente estas descargas aumentan con la carga del motor y el humo evacuado se mantiene azulado. En caso de insinuarse un calentamiento, su caudal se hará anormal para la carga del momento y su aspecto cambiar haciéndose pardusco.
Cuando un engrane de pistón es producido por fugas en el circuito de refrigeración, también puede mezclarse vapor de agua con el humo y hacerlo blanquecino.
Desde el momento en que se constata un desahogo excesivo de gases, debe reducirse la velocidad del motor e incluso prever su detención en el más breve plazo. 
Figura 22-5 – ANEXO 22-4
___________________________________________________________________________________

AGENTES CONTAMINANTES DEL LUBRICANTE
Los aceites lubricantes tanto química como físicamente, deben ser aptos para ser utilizados en un motor. Estas propiedades se determinan mediante pruebas de laboratorio y siguiendo estrictas normas de calidad.
En orden de su importancia, aproximadamente, las pruebas son:
a) Viscosidad.
b) El punto de derrame.
c) Residuo de carbono.
d) Punto de inflamación.
e) Agua y sedimento.
f) Acidez / TBN,
g) Emulsión.
h) Oxidación.
i) Cenizas.
j) Azufre.
El color del aceite no tiene relación con sus propiedades lubricantes.
➽ Los contaminantes más usuales del aceite utilizado en motores diésel marinos son:
👉Partículas de carbón: producto de una combustión incompleta, estas partículas se van endureciendo por las altas presiones y temperaturas.
👉Agua: modifica la viscosidad y a partir de cierta proporción produce
emulsión. El agua puede ingresar a través de los gases de la combustión (en los arranques con motor frío) o por humedad ambiente cuando el motor está parado. También se puede producir el ingreso de agua por contaminación en los circuitos de refrigeración por junta de tapa de cilindros soplada o en los enfriadores con motor parado. En los motores de cárter seco, por ingreso de agua de sentina por el cielo o tapa del tanque correspondiente.
👉
Dilución con combustible: producto de una combustión incompleta, el lubricante pierde viscosidad y baja su temperatura de auto inflamación.
👉Acidez: estos se producen por la formación de ácidos por productos indeseables de la combustión como por ejemplo el azufre.
👉Partículas metálicas: estas producidas por el desgaste en el funcionamiento del motor o durante el
asentamiento del mismo, luego de una reparación.
👉Partículas aspiradas por el motor: provenientes del ambiente en donde está en servicio el motor.
Salitre, arena, humedad, contaminación ambiental.
👀 - CONTROLES DE CONTAMINANTES A LLEVAR A CABO DURANTE LA NAVEGACÍON:
Solo se pueden realizar análisis de dilución, residuo carbonoso, emulsión y, si se cuenta con los
materiales necesarios, determinación del T.B.N. (Total Basic Number o acidez en el aceite).
Se llama
emulsión a la contaminación del lubricante con agua.
El método más utilizado es el de la cucharita que consiste en calentar una cuchara con un mechero o encendedor y luego agregar una gota de aceite a la cuchara. Si el aceite comienza a crepitar está contaminado. Habrá que efectuar comprobaciones adicionales y, dadas el caso, un cambio de aceite.
Para determinar el residuo carbonoso se derraman unas gotas de aceite sobre un papel secante y luego
se compara el dibujo dejado con los que figuran en el NOCEM de lubricantes o en el DYNUMCEN.
Las imágenes 1 y 2 muestran aceite motor, que se puede seguir utilizando.
Imagen 3 presenta aceite que se debe cambiar dentro de poco. Las imágenes 4, 5 y 6 requieren un cambio de aceite inmediato.
VER TAMBIEN AQUÍ ___________________________________________________________________________________
NORMAS PARA EL USO Y CONSERVACION DEL MATERIAL DE CASCO,ELECTRICIDAD Y MAQUINAS NAVALES (N O C E M) CAPITULO 23 LUBRICANTES Y SISTEMAS RELACIONADOS
METODO PARA LA DETERMINACION RAPIDA DEL CONTENIDO DE CARBON EN UN
ACEITE DE MOTORES DIESEL
Los aceites lubricantes de motores diesel contienen aditivos o sustancias activas que mantienen en
suspen sión los residuos de la combustión, distribuidos en partículas finísimas, impidiendo que se
depositen en el motor. A esta característica se la denomina efecto detergente-dispersante.
Se ha comprobado experimentalmente que los aceites usados en motores diesel, con un contenido de
mate rias carbonosas en suspensión superior al 1,5% pueden ocasionar averías, ya que tal
concentración permite la floculación de las partículas carbonosas (proceso de conversión de una
suspensión finamente pulverizada de carbón en partículas de un tamaño tal que se produce una rápida
sedimentación) y su aglomeración como precipitaciones en distintas partes del motor.
En aceites detergentes con dicha concentración carbonosa, se produce también una pérdida de las
propieda des dispersantes del aditivo, generándose el fenómeno citado.
La manera de poder determinar o conocer el estado de ensuciamiento de un aceite lubricante de
motores die sel y la presencia de agua o de combustible, es decir, su dilución y capacidad remanente
de detergencia dispersión, es mediante un análisis de laboratorio. No obstante ello, existe un método
llamado "de la gota" que, si bien es cualitativo y no cuantitativo, es perfectamente apto para realizar a
bordo y las indicaciones que brinda son absolutamente válidas. Este método se lleva a cabo de la
siguiente forma:
1. Utilizando una varilla limpia (de vidrio o de alambre), puntiaguda en un extremo, se sumerge en la muestra del aceite, él que debe hallarse a temperatura de servicio.
2. Se vierte una gota de este aceite sobre el centro de una hoja de papel de filtro de trama fina, colocado en posición horizontal, no apoyado.
3. Se deja que el aceite sea absorbido por el papel.
4. Después de dos o tres horas, la mancha y las partículas carbonosas, difundidas a través de la trama del papel, habrán adquirido su aspecto definitivo.
El ensayo de la gota sobre papel de filtro permite conocer el estado de ensuciamiento, la presencia de
agua o de combustible y la capacidad de detergencia-dispersión que todavía se dispone. Del conocimiento de todas estas circunstancias puede apreciarse de manera aproximada el estado de la carga de aceite del motor. Sin embargo: UN ENSAYO DE LA GOTA NUNCA PUEDE CONSIDERARSE COMO SUSTITUTO DE UN ANALISIS DE ACEITE.
La muestra de aceite para el ensayo debe tomarse del circuito de lubricación estando el motor en
marcha, haciéndolo siempre del mismo lugar y en los periodos que determine el Jefe de Cargo, siendo
conveniente que no se superen, entre muestras, las cien horas de funcionamiento del motor.
Las hojas de papel de filtro, en las que queda la constancia de cada prueba, se deberán archivar en
una carpeta para su conservación y comparación con muestras posteriores.
Para que los diferentes ensayos sean comparables entre sí, es necesario emplear siempre papel
filtrante de la misma calidad.
En la mancha formada se observan las siguientes zonas:

- Una parte central cuya opacidad caracteriza el grado de suciedad del aceite usado en relación con su con tenido de materias carbonosas.
- Una aureola más o menos marcada, que delimita bastante bien la parte central y representa, en cierta manera, el "frente de desplazamiento" de las partículas hacia el exterior de la mancha.
- Una zona de difusión, más o menos oscura, que caracteriza el poder dispersante del aceite
detergente. La regresión o desaparición de esta zona, en el caso de un agente detergente en servicio,
indica una flocula cion de la suspensión y como consecuencia, un mayor riesgo de ensuciamiento del
motor.
- Una zona traslúcida embebida de aceite y desprovista de materias carbonosas. Esta zona toma a
veces una coloración algo amarillenta que estaría relacionada con el estado de oxidación del aceite o
con la presencia de fracciones oxidadas de combustible.
Las partículas de suciedad son más pequeñas que los poros o capilares del papel, lo que explica el
acentuado efecto de difusión en la zona externa.
A medida que se atenúa el efecto de dispersión, las partículas de suciedad van agrupándose y
obstruyen los capilares y el núcleo de la gota depositada sobre el papel adquiere un color más oscuro.
Cuando el borde de la gota adquiere una forma desigual, a modo de radios, indica la presencia de
agua o de combustible en el aceite lubricante.
Las siguientes figuras son una comparación aproximada de distintos resultados que se pueden obtener
con el ensayo de la gota:

En la figura de arriba, el aceite presenta poca contaminación. El núcleo de la mancha se presenta
claro ( 1), mientras que la corona está ligeramente ennegrecida (2).
En esta figura se observa un awnento de la contaminación, pero el aceite todavía tiene una buena
capacidad de dispersión. El núcleo y la corona de la mancha están más oscuros que en la figura
anterior.Aquí se observa que la contaminación ha llegado a su límite, aunque el aceite todavía tiene alguna
capacidad de dispersión. Se deberá efectuar un análisis de aceite e ir previendo un cambio del mismo.
El núcleo y la corona de la mancha muestran el mismo ennegrecimiento
La mancha muestra que la contaminación es demasiado elevada (contenido de carbón superior al
aceptable). La capacidad de dispersión del aceite está agotada. Se debe cambiar indefectiblemente el
aceite del motor. El diámetro interno de la corona de la mancha se ha reducido "apretando" al núcleo,
el cual está fuertemente ennegrecido.
El aceite del motor está diluido con combustible. Se deberá efectuar un análisis del aceite para
verificar el porcentaje de la dilución y determinar la necesidad de su cambio. El tamaño de la corona
de la mancha no ha cambiado, pero está dispersa y sin núcleo definido.
El aceite del motor contiene una cantidad importante de agua. Se deberá efectuar un análisis de aceite
para determinar el contenido de agua y la comprobación de si ésta es dulce o de mar, para actuar en
consecuen cia. El diámetro interno de la corona es más pequeño que el tamaño normal de un núcleo
de mancha. El nú cleo tiene un fuerte ennegrecimiento y su borde está dispersado.
La presencia de agua y/o combustible, tal como se aprecia en las dos últimas figuras, se evidencia
cuando el borde del núcleo de la mancha adquiere una forma desigual, a modo de radios. La
diferencia en las manchas entre contaminación con agua o combustible, o ambos, es difícil de definir;
por lo que de aparecer estas ca racterísticas, deberá completatse este ensayo mediante pruebas de
presencia de agua y dilución por combustible.
___________________________________________________________________________________
👀 - DETERMINACIÓN RÁPIDA DE LA DILUCIÓN DEL ACEITE CON CAJA DE PRUEBAS "MTU"
El aceite motor debe tener una temperatura de unos 20 a 30 ºC lo que se averigua con un termómetro.
Obturar la tobera del viscosímetro con el dedo y echar aceite motor en el mismo hasta derramarse.
Esperar hasta que la muestra quede exenta de burbujas, quitar después, mediante el rascador de plástico, el aceite que se encuentra por encima del borde de la copa.
Ahora retirar el dedo de la tobera del viscosímetro accionando al mismo tiempo el cronometro.
El periodo de vaciado esta determinado y el cronometro sera parado tan pronto como el “hilo de aceite” debajo de la tobera del viscosímetro quede interrumpido por primera vez.
Comparar el periodo de vaciado medio, resultando de tres mediciones en total, con la tabla de valores limite.
Si fuera preciso, efectuar analisis adicionales y, dado el caso, un cambio de aceite
_________________________________________________________________________________

INVERSIÓN DE GIRO DE UN EJE PROPULSOR, SEGUROS Y ALARMAS.
La inversión de giro de un eje propulsor se puede realizar de tres maneras distintas:
- Invirtiendo el sentido de giro del mismo motor Diesel.
- A través de una caja inversora de marcha.
- Invirtiendo el sentido de giro del motor eléctrico acoplado al eje porta hélice en el caso de la propulsión Diesel-Eléctrica.

INVERSIÓN DE GIRO DEL MOTOR DIESEL PRINCIPAL
La inversión del motor principal en los motores diésel marinos es una función crítica que permite a los barcos cambiar su dirección, lo que garantiza una maniobra suave en los puertos, durante el atraque o en situaciones de emergencia. Este proceso implica alterar la dirección de rotación del motor, que es esencial para controlar los movimientos de la embarcación tanto hacia adelante como hacia atrás.
👉 ¿Qué es la inversión del motor principal?
La inversión del motor principal es el proceso de cambiar la dirección de rotación de un motor diésel marino para permitir que el barco se mueva hacia atrás. Esta función se logra ajustando la sincronización del árbol de levas del motor y el sistema de inyección de combustible, lo que permite que el motor funcione en modo reverso. La marcha atrás es un aspecto crucial del sistema de propulsión de un barco, especialmente para maniobrar en espacios confinados como puertos o durante las operaciones de atraque.
👉 Mecanismo de inversión del motor principal
El mecanismo de inversión del motor principal en los motores diésel marinos está diseñado para invertir la dirección de rotación del motor, permitiendo que el barco se mueva hacia atrás. Este es un proceso complejo que implica la coordinación precisa de varios componentes, incluyendo el árbol de levas, el sistema de inversión y los sistemas de control, todos los cuales trabajan juntos para asegurar una inversión suave y eficiente.
👉 Explicación detallada del mecanismo de inversión en motores diésel marinos
El mecanismo de inversión comienza con el ajuste del árbol de levas del motor. En el funcionamiento normal hacia adelante, el árbol de levas controla la sincronización de la inyección de combustible y las operaciones de las válvulas. Cuando se requiere la inversión, la sincronización del árbol de levas se altera para asegurar que el combustible se inyecte en el momento adecuado para que el motor gire en la dirección opuesta. Este ajuste permite que el motor invierta su rotación mientras mantiene una combustión y un rendimiento eficientes.
👉 Componentes Involucrados: Enlace de Inversión, Árbol de Levas y Sistemas de Control
➽Enlace de Inversión: El enlace de inversión es la conexión mecánica que cambia la posición del árbol de levas, permitiéndole cambiar la sincronización de las válvulas para la operación en reversa. Este enlace a menudo es controlado por sistemas hidráulicos o neumáticos para garantizar un movimiento preciso.
➽Árbol de levas: El árbol de levas juega un papel clave en determinar cuándo las válvulas de admisión y escape del motor se abren y cierran. Durante la inversión, la sincronización del árbol de levas se ajusta para permitir la operación en reversa, asegurando que el motor funcione sin problemas en ambas direcciones.
➽Sistemas de Control: Los sistemas de control modernos gestionan todo el proceso de inversión, a menudo integrándose con los controles del puente de mando del barco. Estos sistemas aseguran la posición correcta del árbol de levas y la sincronización de la inyección de combustible, coordinando las acciones complejas necesarias para invertir el motor.
➽ Distribuidor de Aire de Arranque: el distribuidor de aire de arranque es responsable de dirigir el aire comprimido a los cilindros del motor durante el arranque. En el proceso de inversión, juega un papel crucial al controlar el flujo de aire de arranque a los cilindros apropiados para iniciar la rotación en la dirección opuesta. Al dirigir el aire a cilindros específicos en secuencia inversa, el distribuidor de aire de arranque ayuda al motor a comenzar a girar en la dirección deseada, facilitando una inversión suave del movimiento del barco.
👉 Proceso de inversión del árbol de levas
En cualquier motor de combustión interna, el árbol de levas determina cuándo las válvulas de admisión y escape se abren y cierran en relación al movimiento de los pistones. En los motores diésel marinos, cuando se requiere la inversión, la sincronización del árbol de levas debe ser alterada. Al cambiar la sincronización, el árbol de levas asegura que el combustible se inyecte y las válvulas funcionen en sincronía con la dirección de rotación invertida del motor.
Básicamente, en los motores diseñados para la inversión, el árbol de levas está equipado con dos conjuntos de perfiles de levas: uno para la operación hacia adelante y otro para la reversa. Cuando el motor necesita invertir, el árbol de levas se desplaza o rota mecánicamente, alineando los perfiles de levas reversos con las válvulas. Este cambio modifica la sincronización de las válvulas para que coincida con la nueva dirección de rotación del motor. Como resultado, las válvulas de admisión y escape se abren y cierran en intervalos diferentes, correspondientes al movimiento inverso de los pistones. El árbol de levas de inversión permite así que el motor pase sin problemas entre la operación hacia adelante y la operación en reversa.
👉 Importancia de la sincronización de la inyección de combustible en el proceso de inversión
La sincronización de la inyección de combustible es otro factor crítico en el proceso de inversión. El momento preciso en que se inyecta el combustible en el cilindro debe coincidir con la nueva rotación del motor para asegurar una combustión completa y mantener la potencia. Cuando se ajusta el árbol de levas para la operación en reversa, la sincronización de la inyección de combustible también se modifica para que coincida con la nueva sincronización de las válvulas. La sincronización adecuada de la inyección de combustible con la operación de las válvulas es crucial para prevenir golpes en el motor, fallos de encendido o pérdida de potencia durante la inversión. Sin una sincronización precisa de la inyección de combustible, el rendimiento del motor sufriría, lo que llevaría a la ineficacia o daños potenciales.
👉 Descripción General de los Tipos Comunes de Sistemas de Inversión
Los motores marinos pueden estar equipados con diferentes mecanismos de inversión dependiendo de su diseño y requisitos operativos. Cada sistema tiene su propio método para alterar el árbol de levas del motor y la sincronización de las válvulas para facilitar la inversión. La elección del sistema a menudo depende del tamaño del motor, su uso previsto y el nivel de automatización requerido.
➽Inversión Mecánica
Los sistemas de inversión mecánica utilizan engranajes, enlaces o un mecanismo operado manualmente para cambiar la posición del árbol de levas y ajustar la sincronización de las válvulas para la operación en reversa. En este sistema, el movimiento físico de los componentes asegura que el motor pueda invertir su dirección.
Ventajas: Diseño simple, operación confiable y fácil de mantener.
Limitaciones: Requiere intervención manual, lo que puede llevar a tiempos de respuesta más lentos, especialmente en motores más grandes.
➽Sistemas de inversión hidráulicos o neumáticos
Los sistemas de inversión hidráulicos y neumáticos utilizan presión de fluidos o aire para accionar el mecanismo de inversión. Estos sistemas pueden cambiar automáticamente el árbol de levas o ajustar la sincronización de las válvulas controlando el flujo de fluido hidráulico o aire comprimido hacia los componentes accionadores.
Ventajas: Operación más rápida y precisa, ideal para motores grandes que requieren una respuesta rápida. Estos sistemas también pueden ser controlados de forma remota, mejorando la comodidad operativa.
Limitaciones: Más complejos y requieren mantenimiento regular de las líneas hidráulicas o neumáticas. Cualquier falla en el sistema puede llevar a la pérdida de control durante la inversión.
👀 Ventajas y limitaciones de cada sistema
Los sistemas mecánicos son duraderos y simples, pero más lentos y menos adecuados para operaciones automatizadas a gran escala.
Los sistemas hidráulicos y neumáticos ofrecen un control más rápido y automatizado, lo que los hace adecuados para motores modernos y de gran escala, pero su complejidad y necesidades de mantenimiento son mayores.
👉 Pasos involucrados en la inversión de un motor diésel marino
➽Reducir la velocidad del motor a ralentí
Antes de iniciar el proceso de inversión, la velocidad del motor debe reducirse a ralentí o detenerse por completo. Esto garantiza que los componentes del motor, como el árbol de levas y los sistemas de inyección de combustible, puedan ajustarse de manera segura para la operación inversa.
➽Detener el motor
➽Activar el sistema de inversión
Dependiendo del tipo de sistema de inversión en uso (mecánico, hidráulico o neumático), el operador activa el mecanismo de inversión. Esto podría implicar mover el árbol de levas utilizando enlaces manuales o activar de forma remota controles hidráulicos o neumáticos para ajustar el mecanismo de sincronización.
➽Ajustar el árbol de levas para la operación inversa
El árbol de levas se desplaza a su posición inversa, alterando la sincronización de las válvulas de admisión y escape. Este paso asegura que los componentes internos del motor operen sincronizados con la rotación inversa.
➽Reconfigurar el distribuidor de aire de arranque
El distribuidor de aire de arranque se ajusta para dirigir aire comprimido a los cilindros apropiados en la secuencia inversa. Esto asegura que el motor comience a girar en la dirección opuesta cuando se da la señal de arranque.
➽Arrancar el motor en modo inverso
Una vez que el árbol de levas y el distribuidor de aire están configurados correctamente, se reinicia el motor en modo inverso. El aire comprimido se inyecta en los cilindros en la secuencia inversa para iniciar la rotación inversa.
➽Monitorear el rendimiento del motor
Después de que el motor comienza a operar en modo inverso, es esencial monitorear los indicadores clave de rendimiento, como la sincronización de la inyección de combustible, las temperaturas de escape y los niveles de presión para asegurar que el motor funcione de manera suave y eficiente.
👀 Puntos clave a revisar antes y durante la inversión
· Preparación del motor: Asegúrate de que el motor esté a velocidad de ralentí o detenido antes de intentar invertir. Nunca intentes invertir el motor mientras esté funcionando a alta velocidad.
· Funcionalidad del mecanismo de inversión: Verifica que el enlace de inversión, los controles hidráulicos o neumáticos y el árbol de levas estén en buen estado de funcionamiento.
· Sistema de aire de arranque: Verifica que el sistema de aire de arranque esté presurizado y que el distribuidor esté configurado correctamente para la operación inversa.
· Sincronización de la inyección de combustible: Asegúrate de que la sincronización de la inyección de combustible se haya ajustado para la operación inversa para evitar fallos de encendido o pérdida de potencia.
· Retroalimentación del sistema de control: Monitorea cualquier alarma o indicador del sistema de control para detectar posibles problemas durante el proceso de inversión.
· Transición suave: Una vez que el motor esté funcionando en modo inverso, asegúrate de que no haya vibraciones o ruidos inusuales que puedan indicar problemas mecánicos.
👉 Fallas mas comunes en la inversión del motor principal
Desafíos comunes
|
Problemas potenciales
|
Soluciones
|
Fallo del mecanismo de inversión
|
- Falla del sistema mecánico, hidráulico o
neumático. Atasco mecánico, fugas en sistemas hidráulicos/neumáticos o
componentes desgastados.
|
- Inspección y lubricación regular de las partes
mecánicas. Revisar líneas hidráulicas/neumáticas en busca de fugas o pérdida
de presión. Reemplazar componentes desgastados de manera proactiva para
evitar averías.
|
Problemas del sistema de aire
|
- Baja presión de aire o distribuidor de aire defectuoso.
Bloqueos en las líneas de aire que impiden la operación inversa o que causan
ineficiencia.
|
- Monitoreo regular de la presión del sistema de aire de
arranque. Limpiar filtros de aire y eliminar obstrucciones. Asegurar la
calibración adecuada del distribuidor de aire para la operación inversa.
|
Desalineación de la sincronización
|
- Desalineación del árbol de levas o sincronización
de la inyección de combustible. Pérdida de potencia, golpeteo del motor o
combustión incompleta durante la operación inversa.
|
- Revisar regularmente la posición del árbol de
levas y la sincronización de las válvulas. Sincronizar el sistema de
inyección de combustible con la sincronización inversa. Recalibrar el árbol
de levas y el sistema de combustible si persiste la desalineación.
|
Respuesta lenta o inversión retardada
|
- Sistemas de control lentos, especialmente en sistemas
mecánicos o neumáticos antiguos. Retraso en la respuesta de inversión durante
maniobras críticas.
|
- Actualización a sistemas de control hidráulicos o
electrónicos modernos. Mejorar la capacidad de respuesta y precisión de los
ajustes del árbol de levas.
|
Sobrecalentamiento y desgaste excesivo
|
- La inversión prolongada causa sobrecalentamiento
y mayor desgaste. Daño a largo plazo del motor debido a una mala
refrigeración y lubricación.
|
- Asegurarse de que el sistema de refrigeración del
motor funcione correctamente. Revisar y reponer lubricantes regularmente.
Monitorear las temperaturas del motor durante la inversión y evitar la
operación inversa prolongada.
|
👉 Precauciones de seguridad durante la inversión
Asegurar la funcionalidad del
mecanismo de inversión
|
Verifica que el mecanismo de
inversión, ya sea mecánico, hidráulico o neumático, esté en buen estado de
funcionamiento antes de invertir. Revisa el desgaste, las fugas o las
obstrucciones mecánicas.
|
Monitorear la presión del aire de arranque
|
Asegúrate de que el sistema de aire de arranque
tenga suficiente presión para iniciar la rotación inversa. La presión
insuficiente puede llevar a un arranque incompleto del motor en reversa.
|
Verificar la posición del árbol de levas
|
Confirma que el árbol de levas se haya desplazado
completamente a la posición inversa. Un desplazamiento parcial puede provocar
problemas de sincronización o fallos del motor.
|
Comprobar la sincronización de la inyección de
combustible
|
Asegúrate de que el sistema de inyección de
combustible esté correctamente sincronizado con la sincronización inversa
para evitar fallos de encendido o combustiones incompletas.
|
Comunicarte con el puente y la tripulación de la sala de
máquinas
|
Una comunicación clara y precisa entre el puente y la sala
de máquinas es esencial. Todos los miembros de la tripulación deben estar al
tanto de la operación de inversión para asegurar una coordinación fluida.
|
Monitorear los sistemas de control para alarmas
|
Monitorea continuamente los sistemas de control y
alarmas durante la inversión para detectar cualquier problema relacionado con
la sincronización, la presión o los sistemas mecánicos. Responde de inmediato
a cualquier advertencia.
|
Mantener preparados los procedimientos de parada de
emergencia
|
Siempre estar preparado para activar los mecanismos de
parada de emergencia si algo sale mal durante la inversión, como una falla en
el mecanismo de inversión o una pérdida repentina de presión.
|
Asegurar una adecuada refrigeración y lubricación
|
Verifica que el sistema de refrigeración esté
funcionando correctamente y que los lubricantes estén en niveles óptimos para
evitar el sobrecalentamiento durante la inversión.
|
Conciencia y coordinación de la tripulación
|
Una coordinación efectiva entre todos los miembros de la
tripulación involucrados en la inversión es crítica para asegurar la
seguridad y prevenir accidentes. La tripulación debe estar completamente al
tanto de sus roles durante las operaciones de inversión.
|
👉 Avances tecnológicos en el Sistema de inversión de marcha de un motor Diesel propulsor
Avances tecnológicos
|
Detalles
|
Sistemas de inversión electrónicos y automatizados
|
Los controles electrónicos proporcionan ajustes
precisos y automatizados al árbol de levas y a la sincronización de la
inyección de combustible. Reducen la intervención manual y aceleran el
proceso de inversión. Incrementan la confiabilidad al minimizar errores
humanos y fallas mecánicas.
|
Actuación hidráulica y neumática avanzadas
|
Los sistemas hidráulicos y neumáticos avanzados permiten
operaciones de inversión más rápidas, suaves y receptivas. Los actuadores de
alto rendimiento mejoran el tiempo de transición entre adelante y reversa.
Proporcionan mejor control durante maniobras críticas.
|
Monitoreo y diagnóstico digital
|
Las herramientas de monitoreo digital ofrecen
evaluaciones de rendimiento en tiempo real. Detecta problemas como
desalineaciones de sincronización o caídas de presión antes de que ocurran
fallas. Mejora la confiabilidad y apoya el mantenimiento predictivo.
|
Integración con el puente y sistemas de control
automatizados
|
La integración perfecta con los controles del puente del
barco permite la operación remota del mecanismo de inversión. Permite el
control preciso y en tiempo real del motor desde el puente. Reduce la
necesidad de intervención manual en la sala de máquinas, mejorando el tiempo
de respuesta.
|
Mejoras de seguridad
|
Los sistemas automatizados activan protocolos de
seguridad durante las operaciones de inversión. Ajustes automáticos a la
velocidad del motor y retroalimentación en tiempo real mejoran la seguridad
operativa. Reduce los riesgos asociados con fallas de inversión.
|
Mejor coordinación
|
Vinculados con sistemas de control de navegación y
propulsión para maniobras coordinadas. Permiten cambios de dirección del
motor más rápidos y precisos. Esencial para maniobrar en aguas congestionadas
o estrechas.
|
👉 Comparación de los Procesos de Inversión en Motores Marinos de 2 Tiempos vs. 4 Tiempos
➽Motores Marinos de 2 Tiempos
Mecanismo de Inversión Simplificado: En los motores de 2 tiempos, el proceso de inversión es más sencillo porque estos motores no requieren ciclos de admisión y escape separados. En su lugar, los procesos de admisión y escape se gestionan dentro de un solo ciclo, lo que facilita la inversión de la dirección del motor al alterar la sincronización de las válvulas y la inyección de combustible.
Ajuste del Árbol de levas: El árbol de levas en los motores de 2 tiempos tiene perfiles de levas distintos para las operaciones de avance y retroceso. Invertir el motor implica cambiar el árbol de levas para que los perfiles de levas de retroceso modifiquen la sincronización de las válvulas de escape y la inyección de combustible.
Distribuidor de Aire de Arranque: El sistema de aire de arranque es crucial para invertir los motores de 2 tiempos. El distribuidor de aire de arranque se ajusta para dirigir aire comprimido a los cilindros adecuados en secuencia inversa, iniciando la rotación inversa.
➽Motores Marinos de 4 Tiempos
Mecanismo de Inversión Complejo: Invertir en motores de 4 tiempos es más complejo debido a que tienen ciclos distintos de admisión, compresión, potencia y escape. Para invertir el motor, el árbol de levas debe ajustarse para asegurar que las válvulas de admisión y escape se abran y cierren en los intervalos correctos para la operación en reversa.
Ajuste del Árbol de levas: En los motores de 4 tiempos, el árbol de levas generalmente tiene dos conjuntos de lóbulos—uno para la rotación hacia adelante y otro para la reversa. Cambiar el árbol de levas permite que el motor cambie entre estos lóbulos, alterando la sincronización de las válvulas para acomodar la rotación inversa.
Sincronización de la Inyección de Combustible: En los motores de 4 tiempos, invertir requiere no solo un cambio en la sincronización de las válvulas sino también un ajuste preciso de la sincronización de la inyección de combustible para asegurar una combustión eficiente durante la operación en reversa. La complejidad de gestionar tanto la sincronización de las válvulas como la de la inyección de combustible hace que invertir en motores de 4 tiempos sea más intrincado que en motores de 2 tiempos.
👀 Diferencias Específicas en el Procedimiento de Inversión
➽Operación del Árbol de levas: En los motores de 2 tiempos, el ajuste del árbol de levas es más sencillo debido a la naturaleza unificada de los procesos de admisión y escape. En contraste, los motores de 4 tiempos requieren un cambio de árbol de levas más intrincado debido a los ciclos separados de admisión y escape.
➽Sincronización de la Inyección de Combustible: Ambos tipos de motores requieren ajuste de la sincronización de la inyección de combustible, pero el proceso es más complejo en los motores de 4 tiempos debido a la necesidad de alinearse con los ciclos de admisión y potencia.
➽Distribución de Aire: El sistema de aire de arranque juega un papel más prominente en la inversión de los motores de 2 tiempos, donde inicia el movimiento inverso. Aunque importante en los motores de 4 tiempos, el proceso generalmente depende más de ajustes mecánicos precisos.
👉 Mantenimiento de sistemas de inversión
Importancia del mantenimiento y la inspección regulares
- El mantenimiento regular garantiza la fiabilidad de los sistemas de marcha atrás durante las maniobras críticas.
- Ayuda a identificar los primeros signos de desgaste o mal funcionamiento, evitando averías importantes.
- Mejora la seguridad y prolonga la vida útil de los componentes clave.
👀 Componentes clave que se deben comprobar periódicamente:
➽Árbol de levas:
- Inspeccione los perfiles de leva para ver si están desgastados.
- Asegure la alineación del árbol de levas para un cambio suave entre avance y retroceso.
- Mantener una lubricación adecuada.
➽Sistemas de control:
- Inspeccionar las líneas hidráulicas/neumáticas en busca de fugas y obstrucciones.
- Asegúrese de que los enlaces mecánicos estén bien lubricados y libres de desgaste.
- Verifique el funcionamiento del sensor y el actuador en los controles electrónicos.
➽Distribuidor de aire de arranque:
- Monitoree la presión de aire para asegurar un arranque efectivo del motor en reversa.
- Verifique la calibración del distribuidor de aire para el funcionamiento inverso.
- Líneas de aire limpias para evitar obstrucciones.
👉 Estrategias generales de mantenimiento preventivo
- Inspecciones programadas: Realice inspecciones periódicas del árbol de levas, los sistemas de control y el distribuidor de aire.
- Lubricación y controles de fluidos: Mantenga los componentes correctamente lubricados y asegúrese de que los niveles de fluidos hidráulicos/neumáticos sean adecuados.
- Calibración y pruebas: Pruebe y calibre regularmente el cambio del árbol de levas, el distribuidor de aire y los sistemas de control.
- Reemplazo proactivo de componentes: Reemplace los perfiles de levas desgastados, las líneas hidráulicas o los enlaces mecánicos antes de que causen fallas.

INVERSIÓN DE GIRO DEL EJE CON CAJA INVERSORA / REDUCTORA
La inversora permite reducir la velocidad de giro del motor para adecuarla a la hélice instalada, además de invertir el giro y por tanto disponer de marcha atrás. La inversora es un mecanismo fiable capaz de transmitir de forma eficaz la potencia del motor hasta la hélice para que ésta pueda girar en ambos sentidos y con una reducción en su régimen de giro acorde a las características de la hélice instalada. La velocidad de giro de los motores es demasiado elevada y por ello necesitamos reducirla para ajustar el régimen de giro del motor con el del eje de la hélice de tal modo, que a velocidad de crucero, el motor vaya a las “rpms” en la que funciona mejor o sea su par máximo. La segunda función fundamental de la inversora es la de poder invertir el sentido de giro de la hélice y así disponer de marcha atrás, una posición neutral y marcha avante.

Existen diferentes soluciones adaptadas a diferentes barcos y potencias de motorización. Desde la reductora totalmente mecánica, a las que son operadas de forma hidráulica, y hasta con sistemas de transmisión totalmente hidráulicos en donde la potencia es transmitida por el flujo de un aceite movido por una bomba conectada a la salida del motor que es enviado a traves de unos conductos de alta presión, hasta una turbina conectada en el eje de transmisión en cuyo extremo se encuentra la hélice.
Conocido como "V" drive por permitir un ángulo parecido al de la letra "V", entre la entrada y la salida de potencia. Es ideal para conseguir invertir el sentido de la transmisión de potencia.
Diferentes sistemas con diferentes tecnologías y de diferentes fabricantes. Por ejemplo, la transmisión de potencia puede efectuarse de forma lineal o con un ángulo. Existen barcos en los que la disposición de la bancada del motor y la salida de la hélice requieren que la potencia transmitida necesite un cambio de sentido, es lo que se conoce como “V Drive”. Estas transmisiones en “V” hacen también las veces de reducción en el régimen de giro, y también ofrecen la función de inversión de giro para la marcha atrás.
👀 El cuidado de la inversora
Lo cierto es que el mantenimiento de una inversora de pequeño tamaño, requiere simplemente comprobar una vez al año el nivel del aceite de la caja, que permite que todos los piñones funcionen con su correcta lubricación. Para ello, el tapón de plástico por el que rellenar si fuera necesario un poco de aceite, tiene una pequeña varilla con dos marcas de nivel para dejar la caja en su nivel adecuado.
Nunca debemos sobrepasar el nivel superior pues el esfuerzo de mover el aceite en el interior de la caja produciría enormes pérdidas de potencia por fricción del aceite y un gran calentamiento en la inversora. Si nos pasamos de líquido, sin duda debemos aspirarlo para dejar el nivel en su justa medida.
Las inversoras más utilizadas, a diferencia de la "V"Drive, tienen la salida al lado de contrario de la entrada, quedando interpuesta entre el eje de la hélice y el motor del barco. Existen muchos modelos, alguno de los cuales ofrecen un ligero ángulo de salida respecto al eje de entrada (la primera de la izquierda), y dependiendo de su tamaño y potencia tendrán asistencia hidráulica para su manejo.
A partir de los 50 ó 70 CVs, las reductoras o inversoras suelen tener bombas de aceite interna para generar presión con la que controlar sus mecanismos, y este aceite se calienta por lo cual necesitan un sistema de refrigeración, que sumado con los mecanismos de inversión de giro, acaban por complicar la ingeniería de estos elementos.
Como se trata de una reducción mecánica, esta viene fijada por sus engranajes y por tanto no es posible modificar, a no ser que cambiemos toda la reductora. Y es por esta razón, por la que si tenemos que “afinar” el rendimiento de nuestro barco, tengamos que cambiar de tamaño o paso de hélice, más sencillo que tener que cambiar toda la reductora, lo cual sin duda sería otra opción pero mucho más cara.
Un fabricante de reductoras ofrecerá un mismo modelo en diferentes relaciones de reducción por ejemplo 1,5:1 o bien 2,2:1, o incluso con reducciones más elevadas como por ejemplo 2,6:1. Pero existen muchas soluciones mecánicas de muchos fabricantes, por ejemplo para barcos de grandes potencias y con hélices de paso variable existen transmisiones que ofrecen diferentes “marchas” o factores de reducción que permiten ajustar el régimen de giro de la hélice y por tanto el rendimiento del barco al tipo de trabajo que vaya a realizar.
👀 ¿Cómo funciona la inversora?
La inversión en la dirección de giro se logra mediante un mecanismo de doble embrague (en la mayoría de los modelos) que permiten elegir entre dos ejes que giran en sentidos contrarios. Diferentes fabricantes ofrecen diferentes soluciones, pero el esquema propuesto en la figura explica el funcionamiento de la gran mayoría de ellos.
En el acoplamiento a la salida del motor (1), la conexión se establece a través de un disco con acoples de goma que favorece la suavidad entre la salida del motor y la entrada a la inversora. Los engranajes (1) y (5) de la izquierda de la imagen, giran siempre en sentidos opuestos y por tanto así lo hacen también los ejes internos (2) y (6) que transmiten la potencia por el eje interior hasta los dos embragues de Avante (en gris) y Atrás (en rojo).
En el sentido de “Avante”, la transmisión se establece (en flechas azules) a través del embrague de avante (2). En Avante es el embrague (2) el que trabaja transmitiendo la potencia a través de la parte exterior del embrague a la corona (3) que mueve el engranaje (4), que a su vez hace girar el engranaje de salida (5) (en gris) en dirección de Avante al eje de la hélice (8).
En esta situación, aunque la parte interna del embrague de "Atrás" gira movida por el eje interno de marcha atrás no transmite el movimiento a la parte exterior de este embrague. Cuando hay que meter la marcha atrás, simplemente bastará con cambiar el estado de estos dos embragues, pasando la potencia de (1) a (5) y por tanto hasta el embrague de Atrás (6) que trasmitirá el movimiento a (7) por su corona exterior y este a su vez al engranaje de salida (5) pero que esta vez girará en sentido contrario.
El cojinete de empuje
La fuerza que empuja al barco se crea en las palas de la hélice debido al movimiento y reacción de la masa de agua trasladada.
La hélice es por tanto el primer elemento que “empuja” el barco hacia delante y como está firmemente unida al eje de transmisión, la fuerza de empuje que puede llegar a ser de muchas toneladas en los grandes barcos, es transmitida al eje que gira. El eje de transmisión además de hacer girar la hélice es por tanto el que “empuja” el barco hacia delante. Y esa fuerza de empuje tiene que ser “descargada” al barco en algún elemento mecánico pues en caso contrario el eje acabaría destrozando la inversora o el motor de tanto hacer presión y fuerza.

Es el cojinete de empuje el que transmite el “empuje” de la hélice al barco. Para ello existen diferentes modelos en el mercado, algunos de los cuales además permiten acoplar el eje con el motor y absorber pequeños desalineamientos entre el eje del motor y el eje de la hélice. Todo cojinete de empuje está formado por un conjunto de rodillos y no bolas, para que la fuerza sea transmitida desde el eje de giro a la parte exterior del cojinete que a su vez está fijo a través de una bancada al casco del barco.
Este pequeño motor y su transmisión carecen "aparentemente" de rodamiento de empuje. La realidad es que tal rodamiento está "incluido" dentro de la inversora, y por tanto es la inversora la que empuja el barco hacia delante, transmitiéndose el empuje a través de los "silent blocks" a la bancada y esta al casco.
En motorizaciones pequeñas en donde la fuerza de empuje generada es pequeña, a veces la reductora actúa como “transmisor” de esta fuerza de empuje y el barco carece de cojinete de empuje, pues este está metido directamente en la misma inversora/reductora.

INVIRTIENDO EL SENTIDO DE GIRO DEL MOTOR ELÉCTRICO ACOPLADO AL EJE PORTAHÉLICE EN EL CASO DE LA PROPULSIÓN DIESEL-ELÉCTRICA.
La propulsión diésel-eléctrica. Es aquella en que los motores diésel de propulsión en lugar de ir directamente acoplados al eje o ejes propulsores accionan alternadores que producen la energía eléctrica necesaria para la propulsión y todos los demás servicios del buque. En concreto la propulsión se efectúa por medio de motores eléctricos situados en la proximidad de la hélice, se evitan los largos ejes de transmisión y se tiene una mayor flexibilidad de diseño.
👉 MOTOR DIESEL-ELÉCTRICO. Las ventajas de una instalación de este tipo son:
- ü La más significativa es que tanto motores primarios como motores eléctricos de accionamiento pueden estar situados prácticamente en cualquier parte del barco y, por lo tanto, la flexibilidad de instalación y disposición a efectos de daños (importantísima en su aplicación a buques de guerra) está garantizada.
- Se pueden unificar los generadores que suministren las necesidades de potencia requeridas, tanto para la propulsión principal como para los restantes servicios.
- Al ser la transmisión de la energía eléctrica por medio de cables, se pueden llevar prácticamente siempre por el recorrido más conveniente y su protección es mucho más simple que cuando, como ocurre en los sistemas actuales, los ejes propulsores son largos, llegando a veces a un tercio de la eslora o más.
- Por otra parte, se prescinde, por su propia esencia, de los engranajes reductores haciendo innecesaria la utilización de hélices de paso variable.
- Otra gran ventaja es la flexibilidad que permite a la hora de diseñar la ubicación de los equipos principales. El motor diésel ya no tiene por qué estar alineado con los ejes, sino que se puede colocar donde sea más conveniente (donde «menos moleste»). Esto permitirá reducir la longitud de la línea de ejes, cuando no su desaparición, como ocurre en el caso de propulsores eléctricos azimutales.
También desde los 80 la industria de los generadores ha evolucionado, mejorando notablemente el diseño de sus componentes, ya sean generadores, transformadores, cuadros, protecciones, etc. pero tal vez el desarrollo más notable sea el de los sistemas de control, gracias sobre todo a la incorporación de la tecnología digital. se han mejorado sustancialmente los reguladores (control de rpm y carga de los motores diésel), la distribución de la carga activa, los reguladores automáticos de voltaje.
Los sistemas de control de la potencia han ayudado más en el proceso, permitiendo optimizar el número de generadores en marcha y ajustando el reparto de cargas. Finalmente, y por encima de todo ello, tenemos los sistemas integrados de control de la generación que, formando parte de los sistemas integrados de control de la plataforma (sICp), gestionan todo el conjunto del modo más eficiente.
👀 ¿Cómo funciona?
La transformación de la corriente eléctrica generada en el alternador (a una frecuencia y tensión fijas) en otra que, previamente controlada, alimentará el motor eléctrico de CA para proporcionar la potencia deseada en cada momento se realiza de la siguiente forma:
— Etapa rectificadora. Convierte corriente alterna en continua. Hay diversas topologías usando distintos dispositivos. Conlleva también una fase de filtrado.
— Etapa de «alisado». Mediante filtros y condensadores suprime al máximo el «rizado» de la CC producida.
— Etapa inversora. Mediante los dispositivos de conmutación de alta potencia y con diversas topologías, convierte corriente continua en alterna de frecuencia y tensión variables y controlables.
En una palabra, para invertir el sentido de giro del eje, el sistema de control en respuesta a la demanda del control de potencia, invertirá la polaridad en el motor eléctrico acoplado a la hélice de una forma controlada, segura y progresiva.

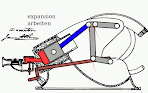
